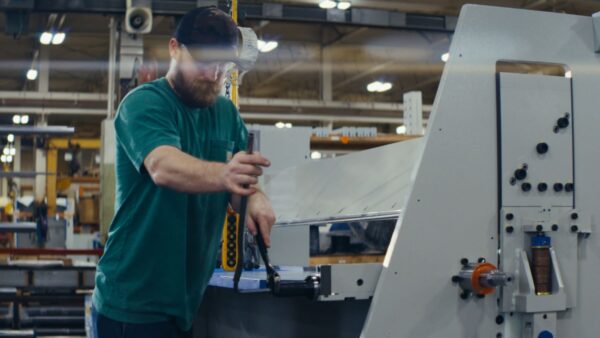
Roper Whitney of Rockford, IL has been producing quality tools and equipment that have been changing the shape of sheet metal since 1910. Behind our extensive history and expansive range of products stands our employees, keeping the gears turning and wheels rolling from the shop to the desk.
We value our employees, continuously strive to make our company a great place to work, and believe in taking care of our team. That’s why we offer a comprehensive benefits package designed to support your health, wellbeing, and professional growth. From competitive pay to career advancement opportunities, we’re committed to helping you thrive in every aspect of your career.
Our currently available positions are listed below. If you are looking for a career with Roper Whitney, please email your resume to hr@roperwhitney.com. A $500 sign-on bonus is available for all positions.
Current Openings
Pay Range: $17.50 – $22.00 per hour
PURPOSE/FUNCTION/SUMMARY (TRAINING NEEDS)
Under general supervision, the General Laborer will be responsible for paint prep and pulling parts for Assembly and 2nd shift. The General Laborer may also be responsible for performing additional duties not stipulated below. If so, these duties are specified on an as needed basis.
ESSENTIAL FUNCTIONS
Paint Prep:
- Prepare equipment to be ready for painting, deburring, tapping, sanding, etc.
- Operated various power tools, including sanders and grinders, to prepare and finish surfaces according to specifications
- Utilized overhead and mobile cranes to safely lift, move, and position heavy materials and equipment
- Applied bonding agents and sealants to surfaces and joints to ensure proper adhesion, waterproofing, and structural integrity
General Labor:
- Assist Assembly by pulling parts from Warehouse and putting parts away in the Warehouse.
- Performs other duties as specified.
KNOWLEDGE, SKILLS AND ABILITIES REQUIRED
- Education/Training: High School Diploma or equivalent required.
- Experience/Skills: Ability to use hand tools, grinders, sanders, etc. Effective oral and written communication skills commensurate with the responsibilities of the position are required.
Salary Range: $26.45 – $36.00 per hour
PURPOSE/FUNCTION/SUMMARY (TRAINING NEEDS)
The Lead Machinist oversees or performs machine setup and adjustments as needed. Reviews production schedules to estimate labor hours and coordinate job assignments efficiently. Performs setup operations on CNC lathes and milling machines, verify proper tooling is available, and ensures jig and fixture configurations are correctly applied to support precision and repeatability. Additionally, implements daily and weekly preventive maintenance programs for all machine shop equipment to reduce downtime and maintain optimal performance. Follow all safety policies and procedures to ensure a safe and compliant working environment.
ESSENTIAL FUNCTIONS
- Overseeing multi-axis CNC machines and CNC lathes (Swiss lathe included) to produce high-tolerance components.
- Fabricate, install, and utilize jigs, fixtures, and tooling to support accurate and repeatable machining processes.
- Train and mentor machinists and operators on proper machine setup, operation, and safety protocols.
- Troubleshoot machining issues and perform real-time adjustments to tooling, programs, and machine parameters.
- Interpret complex engineering drawings, including GD&T specifications, to ensure precise part production.
- Collaborate with engineering and quality teams to verify that all parts meet design and inspection standards.
- Maintain CNC machines and related equipment to minimize downtime and ensure consistent performance, in collaboration with the maintenance department.
- Contribute to continuous improvement initiatives by recommending process optimizations and tooling enhancements.
- Perform in-process and final inspections using calipers, micrometers, CMMs, and other precision measuring tools, in collaboration with the quality department.
- Lead by example in promoting a culture of safety, quality, and operational excellence on the shop floor.
KNOWLEDGE, SKILLS AND ABILITIES REQUIRED
- High school diploma or GED required; trade school or associate degree in machining or related field preferred.
- 3–5 years of hands-on machining experience, including setup and operation of CNC machines.
- Proficient in reading blueprints, interpreting GD&T, and programming/editing G-code.
- Skilled in the design and use of jigs and fixtures for complex and precision components.
- Demonstrated ability to lead small teams and mentor junior machinists in best practices.
- Strong problem-solving, organizational, and communication skills.
- High attention to detail with a strong focus on quality and process consistency.
- Familiarity with ERP/MRP systems is a plus.
- Performs other duties as assigned to support team and production goals.
Salary range for this position is $23.00 – $35.00 per hour.
1st or 2nd shift available
PURPOSE/FUNCTION/SUMMARY (TRAINING NEEDS)
Program, set-up and operate Star Swiss Style CNC lathe and Haas Live Tooling Lathes.
ESSENTIAL FUNCTIONS
Verifies that all product produced meets customer specifications and is in accordance with Company quality standards.
- Programs, performs set-up and operates CNC lathes.
- Operates variety of machines when needed.
- Reads blueprints and gages.
- Provides assistance to co-workers as needed, in the spirit of teamwork, with the goal of meeting or exceeding customer requirements.
- Supports and promotes a team environment.
- Meets or exceeds all production and quality standards.
- All other duties as assigned by a supervisor.
KNOWLEDGE, SKILLS AND ABILITIES REQUIRED
- Education/Training: High School Diploma or equivalent required.
- Experience/Skills: 1 year of CNC Swiss Lathe programming, set-up and operating experience.
Pay Range: $23.00 – $35.00 plus shift premium
PURPOSE/FUNCTION/SUMMARY (TRAINING NEEDS)
Program, set-up and operate a Toyoda horizontal machining center with Fanuc control.
ESSENTIAL FUNCTIONS
Verifies that all product produced meets customer specifications and is in accordance with Company quality standards.
- Program, set-up and/or operate machine or multiple machines as required.
- Work with tight tolerances (+ .0005).
- Working knowledge of GD&T.
- Possess higher programming knowledge of Fanuc controls.
- Ability to perform complete set-ups for long and short-term production.
- Ability to read, write and edit Fanuc controls.
- Ability to analyze job orders, blueprints, specification and design data to calculate dimension, tool selection and machine speeds.
- Work with more complex tooling.
- Accurately complete first and last piece inspection according to Company procedure.
- Provide assistance to co-workers as needed, in the spirit of teamwork, with the goal of meeting or exceeding customer requirements.
- Support and promote the team environment.
- Meet and/or exceed all production and quality standards.
KNOWLEDGE, SKILLS AND ABILITIES REQUIRED
- Education/Training: High School Diploma or equivalent required.
- Experience/Skills: Experience reading and following blueprints and proven knowledge and usage of appropriate measuring devices. Minimum 5 years machine operating experience or related experience. Minimum 3 years reading, editing and writing Fanuc controls. Knowledge of Fusion 360 is a plus.
Salary range for this position is $18.00 – $35.00 per hour.
PURPOSE/FUNCTION/SUMMARY (TRAINING NEEDS)
Set up and operate CNC machines.
ESSENTIAL FUNCTIONS
Verifies that all product produced meets customer specifications and is in accordance with Company quality standards.
- Performs set-up and operates vertical or horizontal CNC Mills or CNC Lathes.
- Operates variety of machines when needed.
- Reads blueprints and gages.
- Works with tight tolerances.
- Knowledge of GD&T.
- Ability to perform set-ups for long and short term production.
- Ability to analyze job orders, blueprints, specification and design data to calculate dimension, tool selection and machine speed.
- Work with more complex tooling.
- Provides assistance to co-workers as needed, in the spirit of teamwork, with the goal of meeting or exceeding customer requirements.
- Supports and promotes a team environment.
- Meets or exceeds all production and quality standards.
- All other duties as assigned by a supervisor.
KNOWLEDGE, SKILLS AND ABILITIES REQUIRED
- Education/Training: High School Diploma or equivalent required.
- Experience/Skills: Minimum 1 year of CNC milling or lathe experience. CNC Programming experience is a plus.
Pay Range: $19.00 – $24.00 per hour
$500 sign on bonus available.
PURPOSE/FUNCTION/SUMMARY
As a Customer Technical Support professional at Roper Whitney LLC, you will be responsible for handling technical calls from customers and working alongside field service technicians, the service manager, and the engineering department to troubleshoot any electrical or mechanical issues they may be experiencing. Your expertise will help customers identify a repair strategy that can get their machines back up and running as soon as possible.
ESSENTIAL FUNCTIONS
- Supervise customers with their machines troubleshooting via telephone
- Keep a log of all calls on Internal service software (Hubspot)
- Familiar with a variety of the field’s concepts, practices, and procedures
- Advise on replacement parts needed to repair a machine mechanically and/or electrically
- Program computers for machines in the field (customer or service orders)
KNOWLEDGE, SKILLS AND ABILITIES REQUIRED
- Education/Training: Associate Degree in Computers, Mechatronics, Electrical, or equivalent position experience preferred.
- Experience/Skills: 3 to 5 years of related experience in a manufacturing environment are preferred. Must possess excellent communication, organizational, computer, and interpersonal skills.
$18.00 – $22.00 per hour
We are looking for someone who is just finishing their Mechatronics courses and is ready to join our team. We will train for 4-6 months, then the service technician will travel with another service technician to learn how to install new machines.
RESPONSIBILITIES
- Verifies that all service meets customer specifications and is in accordance with Company quality standards.
- Service new/existing customers by analyzing work orders, conducting tests, investigating complaints, and resolving problems.
- Planning daily travel schedule.
- Establishes service by analyzing requirements; ordering and gathering components and parts; completing installation; performing acceptance tests.
- Maintains rapport with customers by examining complaints; identifying solutions; suggesting improved methods and techniques; recommending system improvements.
- Keeps equipment operating by following operating instructions, troubleshooting breakdowns, maintaining supplies, performing preventive maintenance, calling for repairs.
- Documents service and installation actions by completing forms; reports; logs and records.
- Maintains customer confidence by keeping service information confidential.
- Updates job knowledge by participating in educational opportunities, reading professional publications.
- Accomplishes operations and organization mission by completing related results as needed.
REQUIREMENTS
- Completion of Mechatronics courses.
$500 sign-on bonus available!
Salary range for this position is $20.00 – $35.00 per hour.
ESSENTIAL FUNCTIONS
- Serves customers by installing and servicing machinery and equipment.
- Verifies that all service meets customer specifications and is in accordance with company quality standards.
- Serves new/existing customers by analyzing work orders, conducting tests, investigating complaints, and resolving problems.
- Planning daily travel schedule.
- Establishes service by analyzing requirements; ordering and gathering components and parts; completing installation; performing acceptance tests.
- Maintains rapport with customers by examining complaints; identifying solutions; suggesting improved methods and techniques; recommending system improvements.
- Keeps equipment operating by following operating instructions, troubleshooting breakdowns, maintaining supplies, performing preventive maintenance, calling for repairs.
- Documents service and installation actions by completing forms; reports; logs and records.
- Maintains customer confidence by keeping service information confidential.
- Updates job knowledge by participating in educational opportunities, reading professional publications.
- Accomplishes operations and organization mission by completing related results as needed.
- Around 70% of the time, travel to job sites within the United States and occasionally Canada and Mexico.
KNOWLEDGE, SKILLS AND ABILITIES REQUIRED
- Education/Training: Mechatronics or equivalent.
- Experience/Skills: Strong background in reading electrical schematics and electronics troubleshooting. Must be able to work independently with little to no supervision. Analyzing information; using judgment; developing and maintaining client relationships; equipment maintenance; strong written and verbal communication; quality focus; results driven; supply management.
$60,000 – $120.00 Annual + Commission
PURPOSE/FUNCTION/SUMMARY (TRAINING NEEDS)
Sells for Roper Whitney, Tennsmith and Roll Former to new and existing accounts. Performs sales function for a targeted market. As a Sales Representative, you will play a crucial role in understanding our customers’ businesses and recommending the most suitable machines and solutions to meet their specific needs. Your ability to grasp the intricacies of our customers’ operations and provide tailored recommendations will be essential in driving sales success and building lasting customer relationships.
ESSENTIAL FUNCTIONS
- Initiates and follows up with customers to sell, resolve problems and answer questions through direct contact, correspondence and telephone.
- Identify and pursue new/potential products.
- Receives and processes orders.
- Participates in marketing analysis of assigned products.
- Prospect and sell end users in a specified territory.
- Determines allowance for credit and makes invoice adjustments when appropriate.
- Travels heavily (50% to 70%) in the field to ensure customer satisfaction and to meet company sales goals.
- All travel to have pre-arranged calls with specific goals to be approved by manager prior to departure.
- Achieve stated sales goals and objectives.
- Assists with trade shows.
- Communicate and coordinate all sales efforts with the Inside Sales Person.
- Collaborate with technical and engineering teams to customize solutions if needed to meet specific customer needs.
KNOWLEDGE, SKILLS AND ABILITIES REQUIRED
- Education/Training: B.S. Degree in Business Management or other related field.
- Experience/Skills: Three to five years related experience in a manufacturing environment. Must possess excellent communication, organizational, computer and interpersonal skills. Excellent knowledge of product and manufacturing capabilities required. Willingness to spend bulk of time travelling in the field. Knowledge of metal roofing business is a plus. Experience with sales of CNC Machines is desirable.
$60,000 – $120.00 Annual + Commission
PURPOSE/FUNCTION/SUMMARY (TRAINING NEEDS)
Sells for Roper Whitney, Tennsmith and Roll Former to new and existing accounts. Performs sales function for a targeted market. As a Sales Representative, you will play a crucial role in understanding our customers’ businesses and recommending the most suitable machines and solutions to meet their specific needs. Your ability to grasp the intricacies of our customers’ operations and provide tailored recommendations will be essential in driving sales success and building lasting customer relationships.
ESSENTIAL FUNCTIONS
- Initiates and follows up with customers to sell, resolve problems and answer questions through direct contact, correspondence and telephone.
- Identify and pursue new/potential products.
- Receives and processes orders.
- Participates in marketing analysis of assigned products.
- Prospect and sell end users in a specified territory.
- Determines allowance for credit and makes invoice adjustments when appropriate.
- Travels heavily (50% to 70%) in the field to ensure customer satisfaction and to meet company sales goals.
- All travel to have pre-arranged calls with specific goals to be approved by manager prior to departure.
- Achieve stated sales goals and objectives.
- Assists with trade shows.
- Communicate and coordinate all sales efforts with the Inside Sales Person.
- Collaborate with technical and engineering teams to customize solutions if needed to meet specific customer needs.
- Bilingual
KNOWLEDGE, SKILLS AND ABILITIES REQUIRED
- Education/Training: B.S. Degree in Business Management or other related field.
- Experience/Skills: Three to five years related experience in a manufacturing environment. Must possess excellent communication, organizational, computer and interpersonal skills. Excellent knowledge of product and manufacturing capabilities required. Willingness to spend bulk of time travelling in the field. Knowledge of metal roofing business is a plus. Experience with sales of CNC Machines is desirable.